IKEA needed a new system to streamline the tracking and management of raw materials like timber wood and plants. The goal was to create a seamless interaction platform for vendors and IKEA stakeholders. This project, named Cloudmask, was aimed at enhancing visibility, efficiency, and compliance across their supply chain.
Please note that certain parts of this case study are under a Non-Disclosure Agreement (NDA). Due to the nature of the information related to IKEA’s internal processes and data, specific details and visual assets have been omitted to comply with confidentiality requirements.
Project Overview
- Client: IKEA
- Industry: Retail/Supply Chain Management
- Duration: 3 months
- Role: UX/UI Designer
- Team Size: 8
Challenge
The current process lacked real-time tracking and visibility, making facility management cumbersome and alert systems unreliable. Monitoring transactions and generating compliance reports was also challenging. We needed a solution to address these issues effectively.
1. Discover
We started with stakeholder interviews, surveys with vendors, and analyzing existing supply chain processes. This helped us identify key pain points and user needs, such as the necessity for real-time tracking, efficient facility management, timely alerts, and comprehensive transaction views.
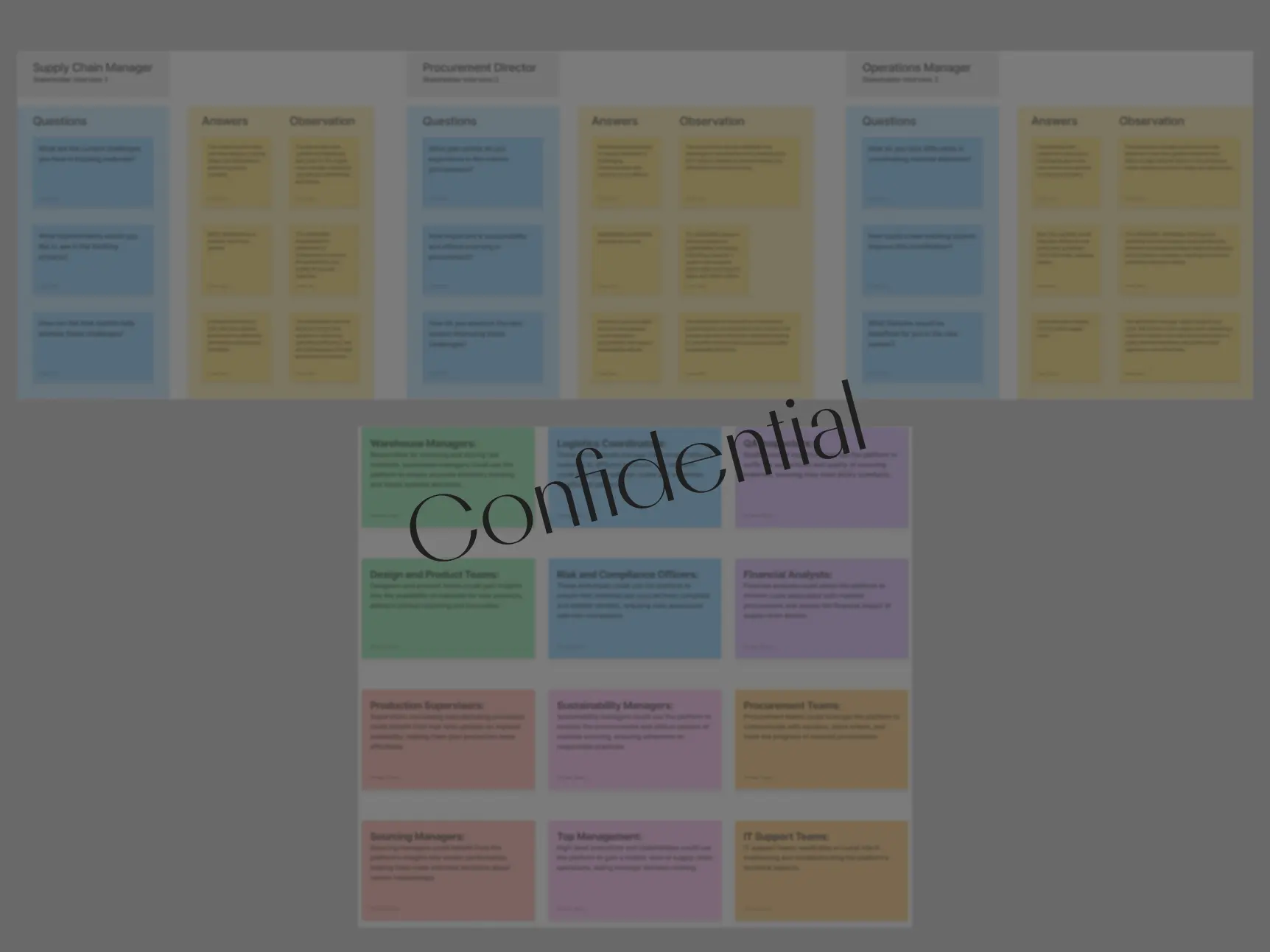
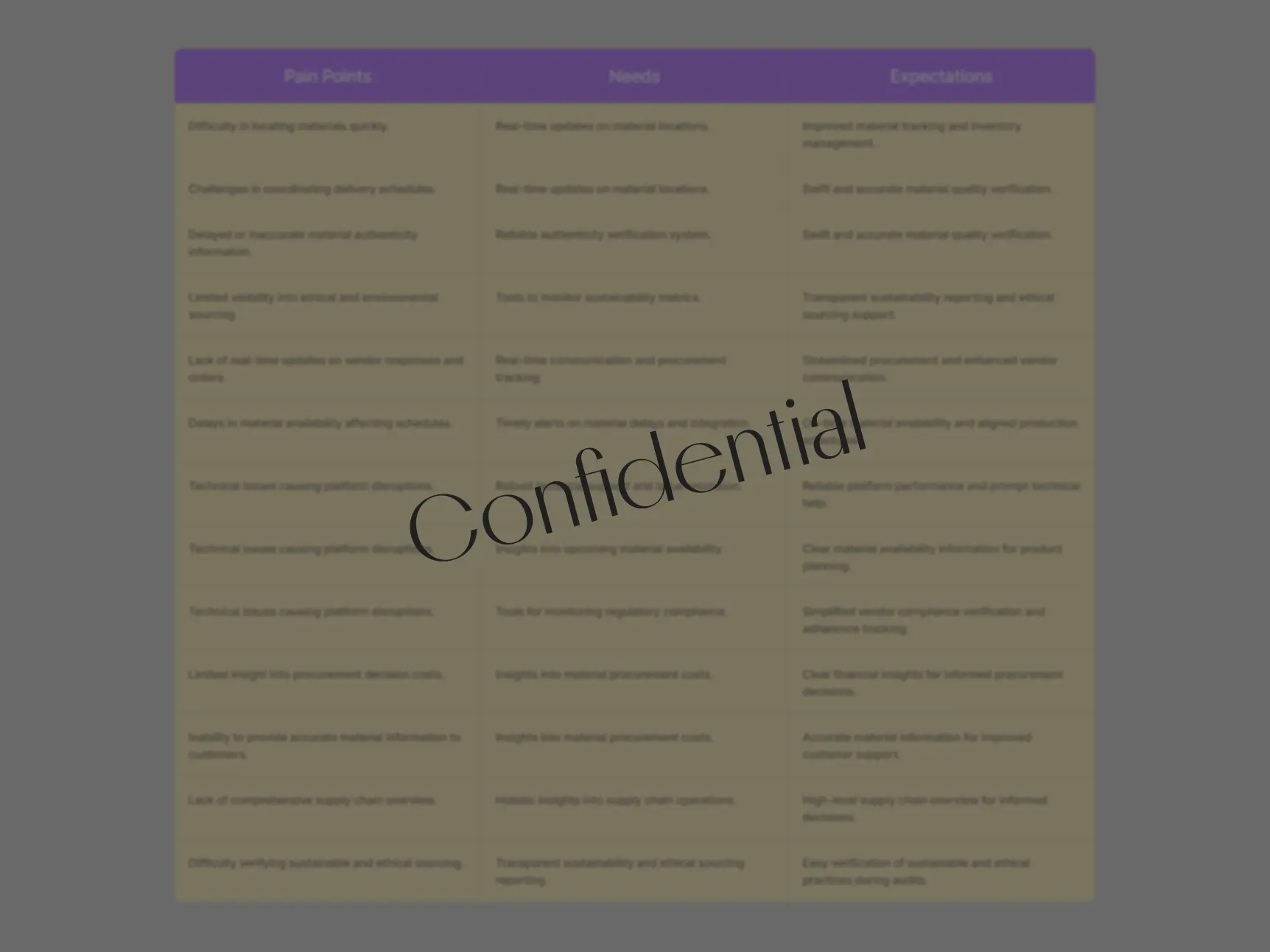
2. Design
After brainstorming sessions, we developed initial sketches and wireframes to visualize the system’s structure and flow. We mapped out user journeys to understand the interactions between vendors and stakeholders with the system.
Transitioning from wireframes to high-fidelity prototypes, we focused on key features:
- Real-Time Tracking: An interactive dashboard to track raw materials.
- Facility Management: Tools for managing storage and processing facilities.
- Alert System: Automated alerts for critical events.
- Transactions: Detailed views of transactions.
- Compliance Reports: Automated report generation.
- We ensured the interface was clean, intuitive, and user-friendly.
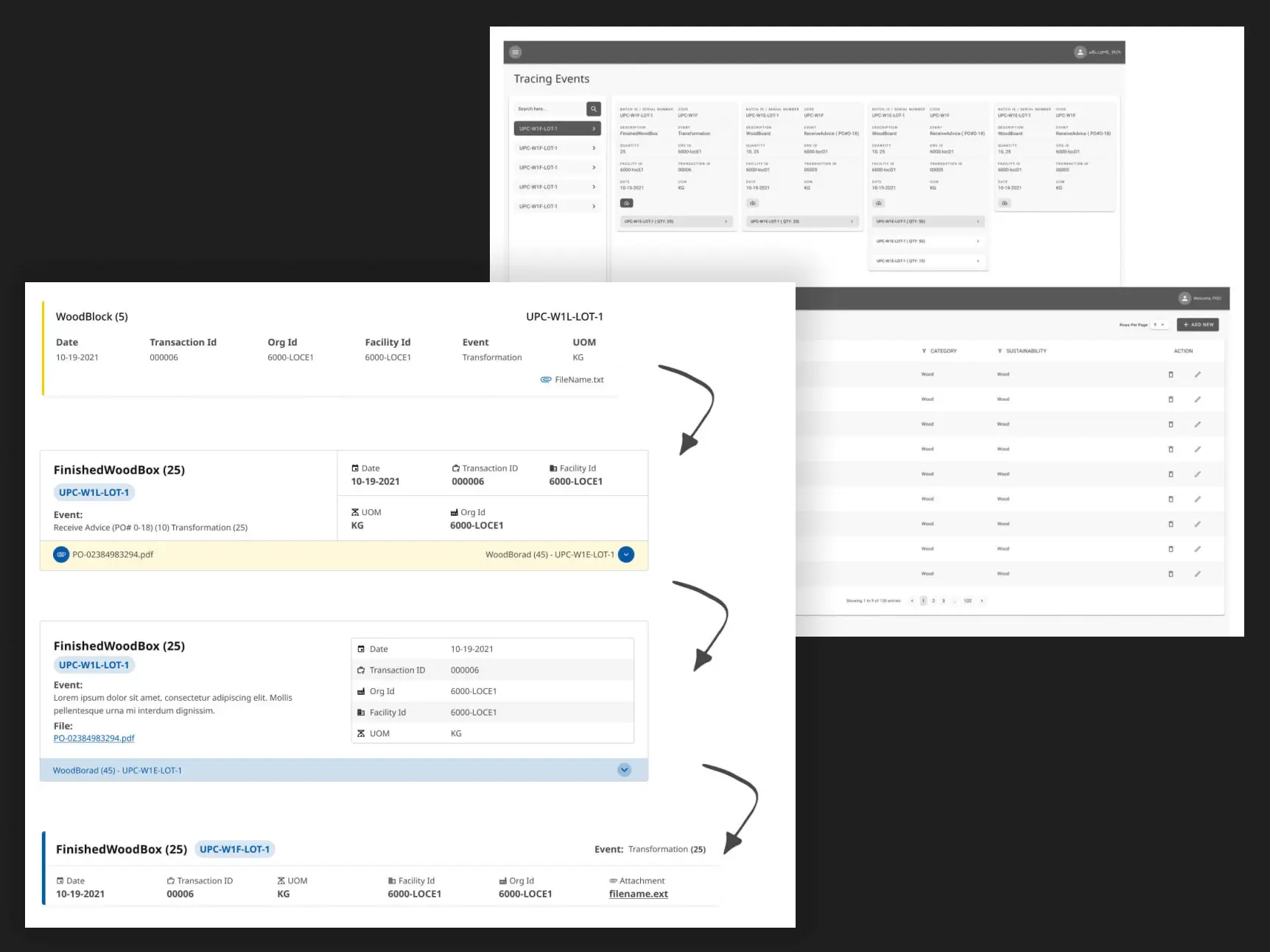
3. Develop
Working in an Agile environment, we closely collaborated with developers, using tools like Jira for task management. Regular stand-ups kept everyone aligned, and detailed design specifications facilitated smooth handoffs.
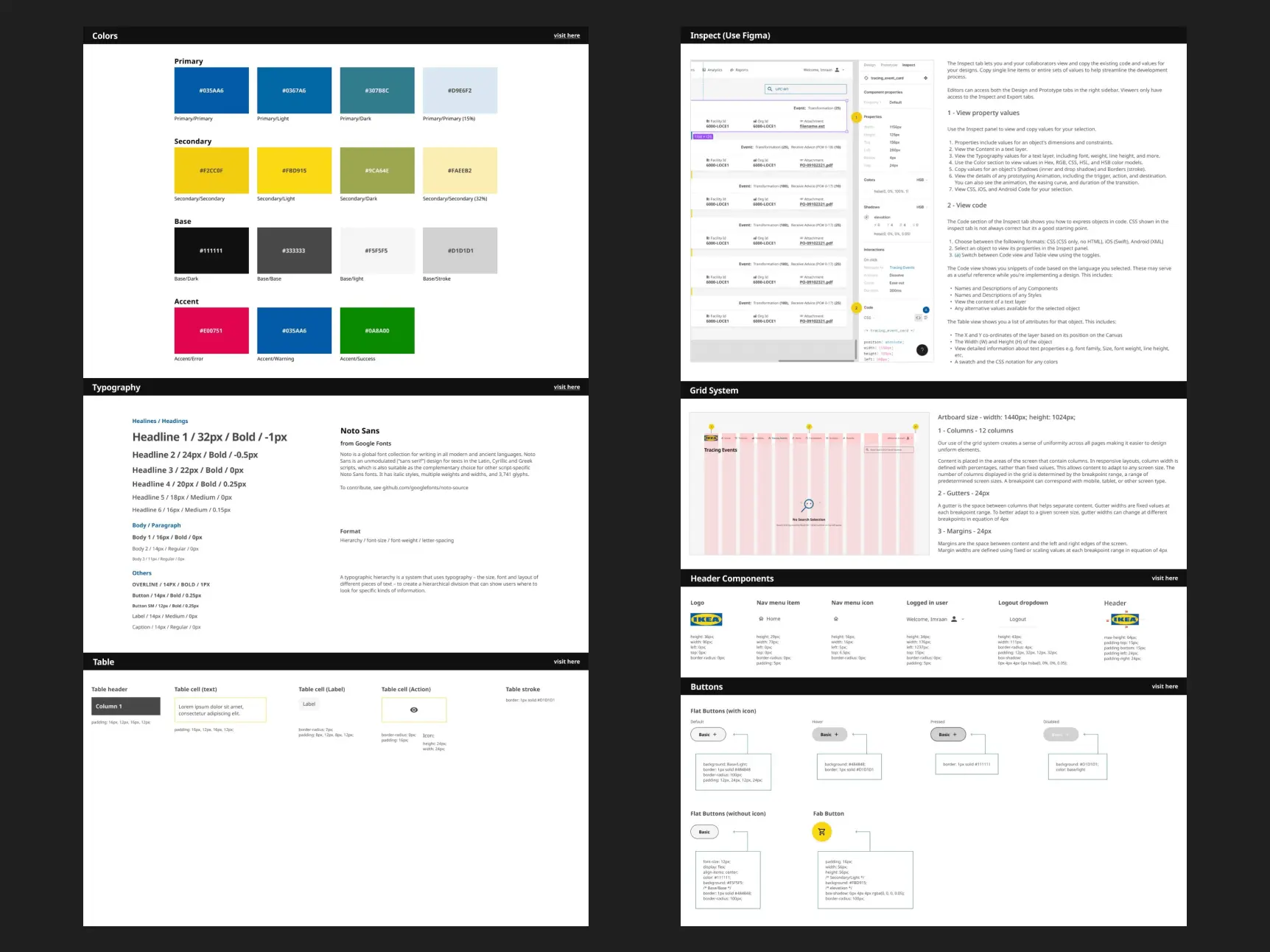
Testing and Iteration
We conducted multiple rounds of usability testing with vendors and stakeholders, iterating based on feedback to refine features and improve usability. The user journeys were simplified, ensuring seamless interaction with the system. We also adhered to WCAG guidelines to make the system accessible and inclusive.
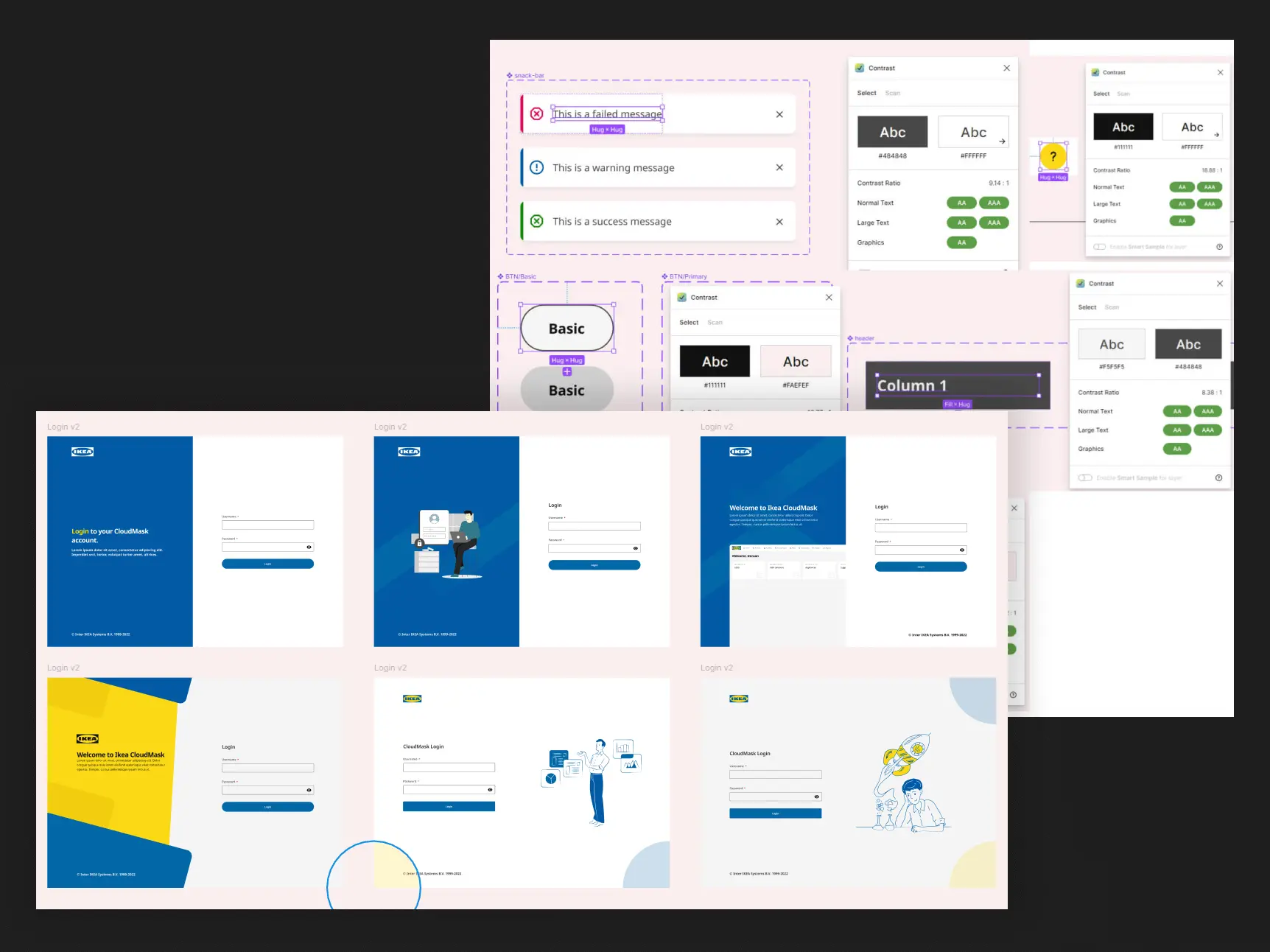
4. Deliver
Outcome:
- Enhanced visibility of raw materials with real-time tracking.
- Improved facility management and operational efficiency.
- Reduced manual effort through automated alerts and compliance reporting.
- Positive feedback from vendors and stakeholders on usability and functionality.
Impact:
- Streamlined supply chain operations.
- Increased stakeholder satisfaction.
- Improved compliance and reporting accuracy.
UX Impact:
- Easier tracking and management of raw materials.
- Better communication and coordination between vendors and IKEA.
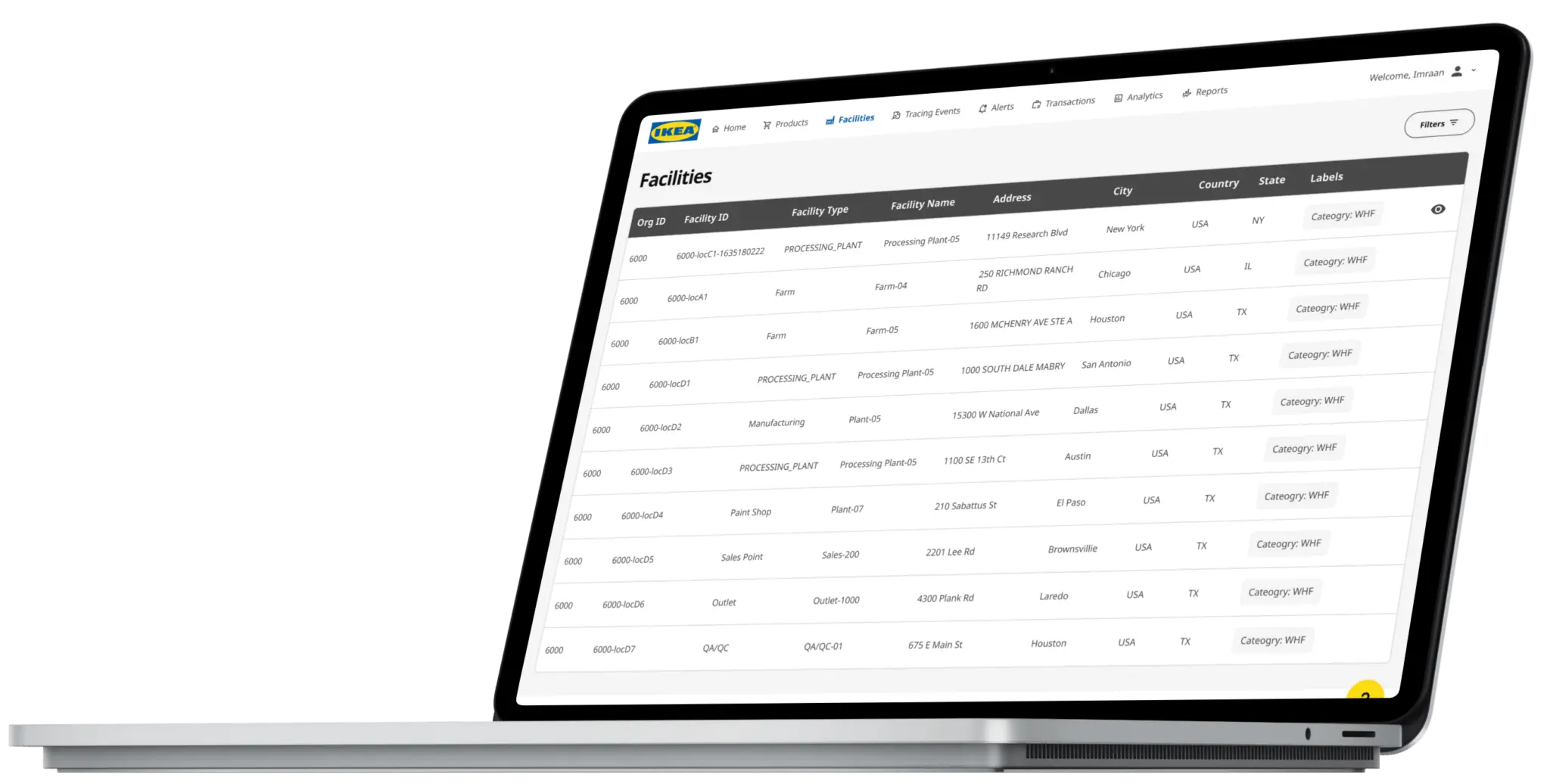
Reflection and Learnings
Challenges Faced:
- Integrating real-time tracking capabilities.
- Balancing detailed functionality with an intuitive user interface.
Lessons Learned:
- The importance of continuous user feedback and iterative design.
- The value of cross-functional collaboration for complex system designs.
Future Improvements:
- Explore integration with IoT devices for more precise tracking.
- Additional customization options for alerts and reports.
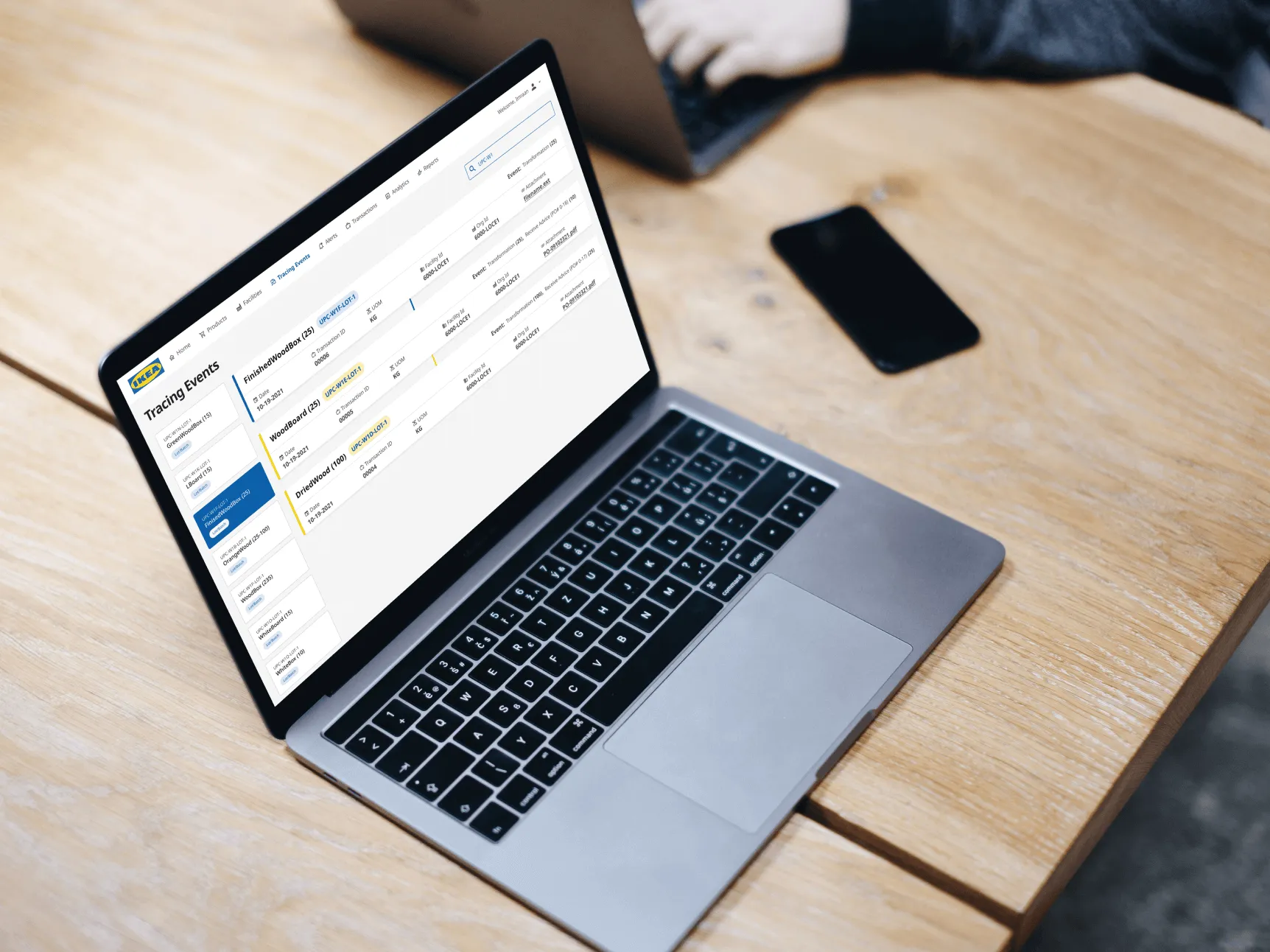
Feedback
“Design expertise was instrumental in creating a system that meets our supply chain needs. The system has significantly improved our operations.”
– IKEA Project Manager
“Tracking and managing raw materials has become so much easier with Cloudmask. The system is user-friendly and highly efficient.”
– IKEA Vendor